CPTU OFFSHORE GEOTECHNICAL INVESTIGATION
- Nardipta Pratama
- Aug 9, 2015
- 5 min read
Marine site investigations should be programmed in such a way as to guarantee that reliable geotechnical data relevant and are available at the various design phases. In specific, the obtained data should be adequate to enable the assessment of the site suitability with respect to the offshore structure and the level of acceptable risks for the foundation and integrity of the offshore structure.
The general objectives of a marine soil investigation are to establish the characteristics and mechanical properties of the seabed soils, and to gather additional relevant knowledge about the site, including geology and stratification, as appropriate. This also includes, when applicable, determining the characteristics of any geohazard features that could impact upon the proposed offshore structure.
The characteristics and mechanical properties of seabed soils are determined from a combination of drilling, sampling and in situ testing, most especially the piezocone penetration test ( CPTU ).
The last 40 years or so has seen significant developments in all aspects related to the use of the CPTU in marine soil investigations. In fact, as offshore drilling is being undertaken in ever increasing water depths, it is hard to imagine a marine soil investigation without CPTU equipment and deployment systems being considered, for performing CPTU’s in expected future water depths of 5000m to 6000m. Typically, a geotechnical investigation is performed after the geophysical investigation has taken place and the results have been examined.
The lack of geophysical data increases the risk from unpredicted problems and resolving differences across the site. The main goal of the geotechnical investigation is to characterize the soil properties by means of in situ tests and samples that are subsequently examined and tested.
The geotechnical properties acquired from the field investigation and subsequent laboratory work provide the basis for the engineering parameters required for design of foundations and other offshore infrastructure.
A geotechnical site investigation is executed by specialized equipment from a purpose built platform. The investigation can be attained by two alternative systems: (a) downhole; and (b) seabed (Figure 1).
A downhole system refers to drilling of a borehole and testing or sampling of the soil by means of ‘’downhole tools’’ that fit through the drill string. This is comparable with the set-up used in the oil drilling industry, where a wide variety of downhole tools are used to characterize hydrocarbon reservoirs at depths of a few thousand metres down drill strings. However, the drilling in a geotechnical investigation needs to be performed in a much more sensitive manner compared with reservoir drilling, and the type of testing is quite different, with evaluation of soft sediments rather reservoir rocks.
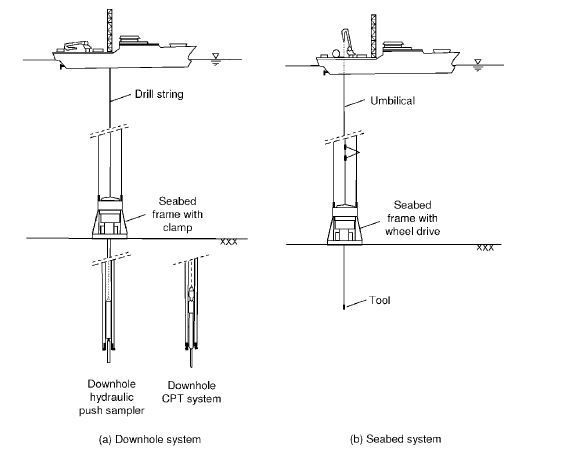
FIGURE 1. Downhole System an Seabed System
The cone penetration test (CPT) is presently the most performed in situ test during a geotechnical investigation, generally using a piezocone that incorporates pore pressure measurement.
The cone penetration test (CPT) is the most widely used in-situ test for marine engineering applications. The main use is providing information on soil type and stratification as well as shear strength in clays and relative density and friction angles in sand.
CPTs have very wide applications which includes:
Offshore oil & gas pipeline route investigations, trenching and stability studies.
Geotechnical investigations for seabed structures and anchors.
Pre-dredge investigations.
Ground truth for geophysical survey and morphological mapping.
Submarine cable route surveys and burial assessment studies.
Inshore / coastal water civil engineering studies.
Technology and sciences
The cone penetration test provides an empirical assessment of seabed soils based on the resistance of the soil to a cone-tipped probe, or penetrometer, as it is pushed into the seabed ata constant rate of penetration (2cms per sec.). Standard cones have a tip angle of 60° and a cross-sectional area between 5cm2 and 20cm2, with 10cm2 and 15cm2 cones being the most common.
In a piezocone penetration test (PCPT), an additional parameter, soil pore water pressure, is measured via a porous element in the cone face or at the shoulder between cone tip and friction sleeve. (The PCPT is sometimes referred to as the CPTU, the u being geotechnical shorthand for pore pressure). Data are transmitted in realtime to the surface support vessel for recording and analysis.
Soil types are determined by reference to a graph of Cone Resistance (qc) against the Friction Ratio. Friction Ratio is the sleeve friction (fs) divided by Cone Resistance (qc). Other empirical relationships are used to estimate shear strength in clays and the relative density and internal angle of friction in sands.
The basic result, i.e. cone resistance, local friction and pore water pressure will be presented after the field investigation is done. Data processing and presentation in the final report will include the corrected tip resistance, corrected sleeve friction, excess pore pressure measure and the corresponding ratios of the corrected values, i.e. friction ratio and Bq.
The piezocone test (CPTU) is a cone penetration test (CPT) with additional measurement of the porewater pressure at one or more locations (U1, U2 and U3) on the penetrometer surface .

FIGURE 2. Piezocone penetrometer (measured parameter)
Cone penetration testing, with porewater pressure measurements, gives a more reliable determination of stratification and soil type than a standard CPT. In addition, CPTU provides a better basis for interpreting the results in terms of mechanical soil properties. Mechanical properties to be assessed are:
shear strength parameters
deformation and consolidation characteristics.
Drilling mode testing (Downhole mode)
The advantage with drilling mode (down-hole) CPT in a drilled borehole is that much deeper penetration than achieved by non drilling mode (sea bed mode) can be reached since the drilling team can penetrate through the hard layers.
When drilling from a drillship, it is important to have good control on the movement of the drill bit by having an efficient and responsive heave compensation system to minimize disturbance in the soil.
The total depth limitation of the downhole CPTU system is approximately 600 - 700 m because of the necessity for an umbilical with hydraulic oil. This depth includes from the drill floor, through the water column and penetration of the sea bed.
AP Vandenberg developed WISON APB as the most popular propriety system is the WISON APB.

Figure 3. Drilling mode CPT system (Lunne 2010)
Piezocone will measure the cone resistance, local friction and the pore water pressure. The thrust will be transferred to the cone by an internal clamping device and the cone will have a base area of 10 square centimeters with penetration rate of 2cm/sec.
During penetration, output signals from the cone tip, the friction sleeve and pore pressure will be recorded on disk and subsequently re-plotted on A4 size paper. Visual display on the monitor during the testing enables the operator observes the results timely, to ensure the quality and accurate results obtain from the penetration. The data acquisition is done every 2cms, while the testing will be conducted every 3m stroke or early termination in the case of hard soil.
The cone is regularly calibrated prior to mobilization and the calibration certificates will be available onboard the vessel.
Reference Geophysical and Geotechnical Techniques for nearshore seabed soils and rock ( a handbook for non specialist-FUGRO), Offshore Geotechnical Engineering Mark Randolph and Susan Gouvernec, guide to marine soil investigations (Gardline Geosciences- B. Georgious )
Comments